Opening
The metal casting and foundry business depends much on a back casting room. The last shape, finishing, and quality control of metal castings happen in this vital area. Back casting rooms enable metal components—in manufacturing, automotive, or aerospace sectors—to be more durable, accurate, and efficient.
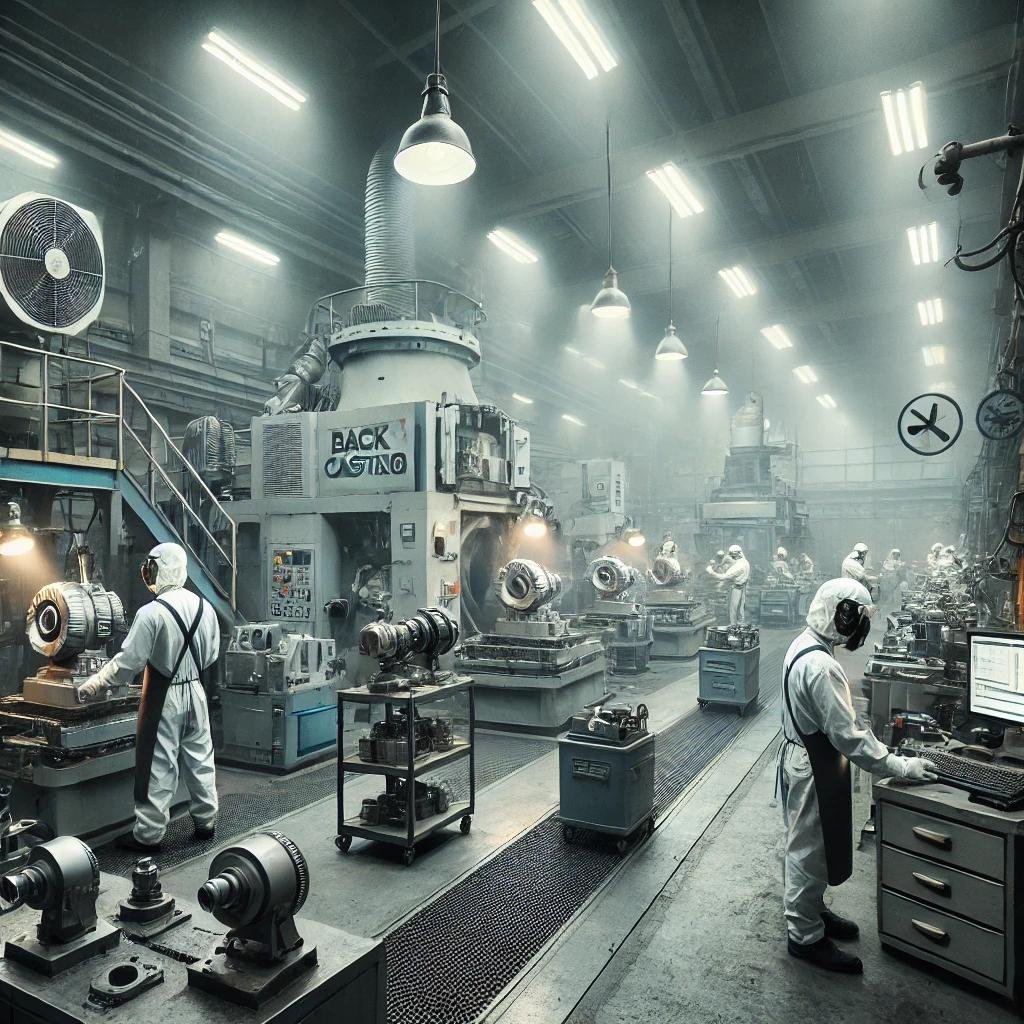
This paper will offer a thorough overview of back casting rooms, their importance, purposes, and best practices for preserving an effective workflow.
Describes a Back Casting Room
Within a foundry or manufacturing plant, a back casting room is a section specifically designed for secondary metalwork operations including grinding, polishing, inspection, and finishing. This area is absolutely essential to guarantee that cast metal parts satisfy the necessary standards free from flaws and faults.
Important Back Casting Room Purposes
- Surface Finishing – Removal of rough edges, extra metal, and imperfections brings the surface finish to be smooth.
- Quality Control & Inspection – Checking cast pieces for flaws including misalignment, porosity, and cracks in quality control and inspection.
- Heat Treatment – Heat treatment helps mechanical qualities including resistance, hardness, and strength to improve.
- Precision Machining – Precision machining is dimensional accuracy achieved using CNC tools and other machinery.
- Deburring & Cleaning – Eliminating extra material from the surface and cleaning the finished good constitute deburring and cleaning.
Value of a Backcasting Room
1. Improving Content Quality
A well-equipped back casting room guarantees the final result satisfies industry requirements. Eliminating flaws and enhancing surface finish help to increase lifetime and usefulness.
2. Increasing Office Productivity
Manufacturers can avoid waste and streamline process by centralizing post-casting activities in a specialized area, therefore lowering production time and costs.
3. Respecting Compliance and Safety
Dealing with metal castings calls for precautions to stop workplace mishaps. Proper ventilation and maintenance of a back casting room assist reduce dust, heat, and sharp metal part risks.
4. Increasing Equipment Lifetime
Correct handling of metal components in the rear casting room and regular maintenance help to minimize damage to machines, therefore extending their lifetime and lowering replacement costs.
Best Practices for a Back Casting Room Designed Effectively
1. Correct Dust Control and Ventilation
Fine particles produced by metal grinding and polishing might be dangerous if breathed. Using dust collectors and installing a good ventilation system helps to safeguard workers and enhance the air quality.
2. Frequent Equipment Maintenance
Consistent performance and minimum downtime are ensured by routine examination and servicing of machinery including grinders, lathes, and polishing tools.
3. Application of Superior Consumables and Tools
Purchasing strong abrasives, cutting tools, and polishing supplies guarantees accuracy in last product finishing and increases efficiency.
4. Safety Tools and Trained Staff
Employees should be taught how to operate machinery properly and use gloves, face shields, and ear protection—personal protective equipment.
5. Lean Manufacturing Idea Application
Reducing waste, organizing the workstation, and streamlining processes improve output and lower running expenses.
Uses for a Backcasting Room
Many businesses depending on metal components make extensive use of back casting rooms:
- Automotive sector – Including brake components, transmission casings, and finishing engine blocks.
- Aerospace industry – Processing turbine blades, airplane components, and landing gear components.
- Building and Infrastructure – Polishing metal parts for pipelines, bridges, and structural frames.
- Medical Equipment Manufacturing – Producing prosthesis and highly accurate surgical tools.
- Industrial Machinery – Guarantees machine part and tool precision as well as longevity.
Typical Back Casting Room Problems and Their Remarks
1. Managing Metal Waste
Challenge: The challenge is inefficiencies brought on by too much metal shavings and dust buildup. Solution: Recycling initiatives and magnetic separators for effective waste control help to solve this.
2. Keeping Constant Quality
Challenge: Variance in finishing techniques might cause uneven product quality. Solution: Standardized processes, automated finishing equipment, and rigorous quality control guarantees consistency.
3. Safety Issues Regarding Workers
Challenge: Health hazards arise from metal particles, noise, and extreme temperatures. Solution: Install noise-reduction devices, offer appropriate PPE, and start safety training courses.
4. Fiscal Control
Challenge: High consumable and machinery maintenance expenses challenge profitability. Solution: Investing in predictive maintenance programs and energy-efficient tools helps to lower long-term expenses.
Often Asked Questions, or FAQs
1. A back casting room serves primarily for what?
Removing flaws, guaranteeing accuracy, and getting items ready for their ultimate usage in sectors like automotive and aerospace help a back casting room mostly refine metal castings.
2. Usually, a back casting room features what kind of equipment?
Among the common tools are grinders, lathes, CNC machines, heat treatment furnaces, polishing tools, and quality control devices.
3. How might a back casting room raise output efficiency?
Manufacturers can lower material waste, decrease mistakes, improve product quality, and optimize workflow by centralizing post-casting procedures, thereby raising their output.
4. In a back casting room, what safety precautions ought to be in place?
Among the fundamental safety precautions are appropriate ventilation, PPE use, frequent equipment maintenance, fire danger avoidance, and worker training courses.
5. In a back casting room, how might producers cut expenses?
By putting automation into use, streamlining processes, making investments in premium but reasonably priced products, and keeping good waste management techniques.
Final Thought
The metal casting business cannot function without a rear casting room since it guarantees that cast components satisfy the best criteria of performance and quality. Manufacturers may keep a competitive edge and improve efficiency by implementing best practices, current equipment investments, and safety top priorities. Optimizing back casting rooms will remain essential as technology develops in order to provide outstanding metal products across a range of sectors.